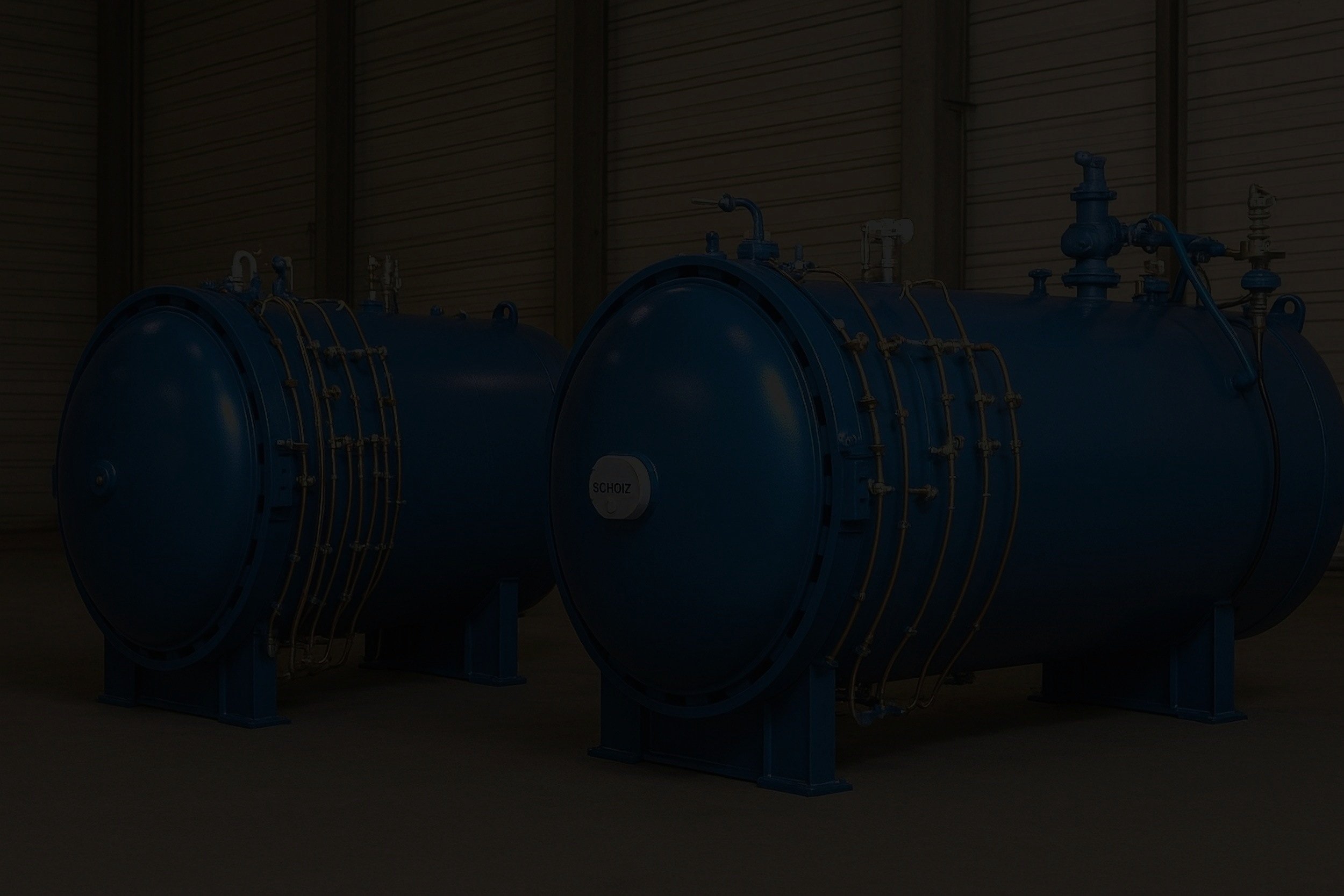
The Solution: Production Simulator
Client: A major aircraft manufacturer
The Challenge
Optimizing a composite manufacturing process presents several hurdles:
It's a complex process involving multiple stages like cutting, lamination, and curing.
The primary bottleneck occurs during batch processing on the curing machines.
There's a wide variety of shared resources, including workstations, cutting machines, and tooling.
The process is highly manual, leading to significant dependence on labor and work shifts.
Frequent replanning is necessary due to constant changes in demand and priorities.
It's difficult to analyze planning quality because of the vast amount of data and key performance indicators.
The Objective
Our goal was to simplify the evaluation of production plans to increase throughput in the sector and optimize the use of labor, machinery, and equipment.
The Solution
We developed a simulator that analyzes production plans by considering:
The availability and capacity of each piece of equipment and each type of labor per shift.
The proposed production plan.
This simulator provides a complete evaluation of the plan, clearly indicating:
Which resources are being underutilized and to what extent.
Which capacity limits are being exceeded and the magnitude of these violations.
Results
Real-time feedback that helps simulate and optimized production plans.
Identification of operational limit violations before the plan execution.
Support for historical performance analysis to pinpoint bottlenecks and continuously improve processes.